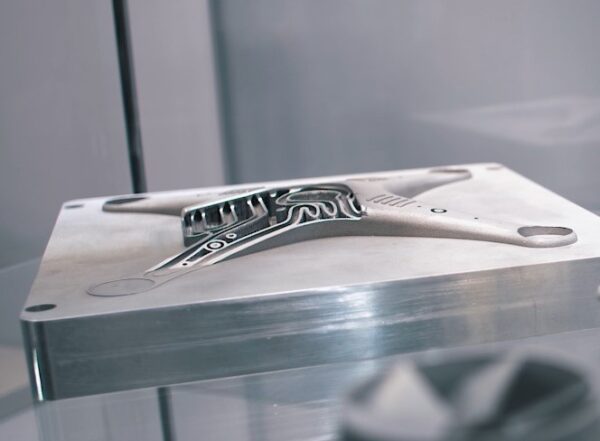
La realidad del taller digital: Fabricación aditiva para el cuadricóptero
Bienvenido de nuevo a nuestra serie de blogs semanales diseñada para mostrarle cómo se desarrolla el concepto de un taller de máquinas digitales en la vida real. Sigue la creación de un juego de moldes de cuadricóptero como una forma de ilustrar cómo funciona un taller de máquinas digitales y por qué es superior a otros enfoques de desarrollo de productos. En esta publicación analizaremos otro aspecto importante de un taller de máquinas digitales: la fabricación aditiva. También conocida como impresión 3D, esta tecnología tiene muchas aplicaciones interesantes, como sin duda sabrá.
Dado que esta serie de blogs ha estado utilizando el desarrollo de un molde de cuadricóptero para ilustrar los beneficios de Digital Machine Shop, me centraré en la fabricación aditiva para moldes, una aplicación en la que esta tecnología ofrece algunas ventajas significativas.
Un proceso de fabricación aditiva deposita material, una capa sobre otra, utilizando como guía la geometría 3D creada en un sistema CAD. El material suele ser un polímero o un metal. El uso de fabricación aditiva de nuestro proyecto de cuadricóptero involucró tanto metal como polímero: metal para construir los insertos de molde con canales de enfriamiento conformados y polímero para crear moldes de plástico de manera económica para abordar lo que se conoce como el «problema de los primeros 200».
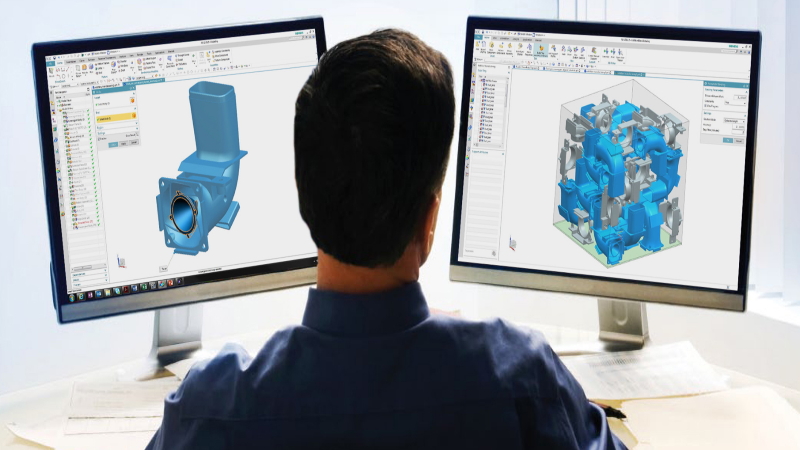
Impresión de moldes de prueba de plástico económicos
Como ha visto en estas publicaciones de blog, aprovechamos todas las oportunidades a lo largo de este proyecto para simular procesos del mundo real utilizando el software de Siemens y la tecnología Digital Twin, aumentando en gran medida nuestras posibilidades de que el resultado sea una pieza perfecta. Pero dado el costo extremadamente alto de los moldes de inyección, dimos un paso más utilizando la fabricación aditiva para la fabricación de moldes para asegurarnos de que no termináramos con una cubierta de cuadricóptero que no encajara perfectamente en el resto del cuadricóptero.
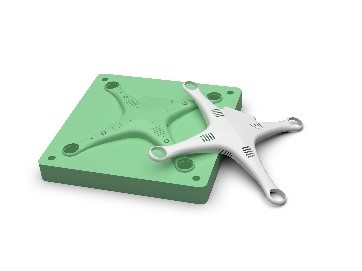
Antes de la disponibilidad de la fabricación aditiva, habríamos construido el molde de inyección de metal real, a un gran costo, y luego producido una pequeña serie de piezas para examinar su ajuste. Si por alguna razón las piezas producidas no fueran válidas, repetiríamos el proceso encargando un nuevo molde. Los moldes de prueba de plástico impresos le permiten iterar de forma rápida y económica en la geometría del molde final. Esto reduce en gran medida la probabilidad de tener que desechar un molde de metal que cuesta cientos de miles de dólares y posiblemente meses de tiempo de entrega.
Para el molde prototipo impreso, utilizamos un proceso de fabricación aditivo basado en polímeros para crear una versión plástica del molde de alta precisión. Si bien no son lo suficientemente robustos para una producción de alto volumen, los moldes de plástico pueden ser adecuados para producir hasta 200 piezas, más que suficiente para determinar si nuestra pieza encajaría en el resto del ensamblaje del cuadricóptero.
Impresión de moldes metálicos para enfriamiento conformado
En la publicación sobre el diseño del molde del cuadricóptero, notamos que prestó especial atención al proceso de enfriamiento del molde. Hicimos esto en parte porque el enfriamiento afecta la calidad de la pieza moldeada (la cubierta muy visible del cuadricóptero, en nuestro ejemplo). Igualmente importante fue el hecho de que el tiempo de enfriamiento tiene un gran efecto en la eficiencia del proceso de moldeo. Dado que un enfriamiento más rápido significa tiempos de ciclo más rápidos, reducir el ciclo de enfriamiento mejora la eficiencia del proceso y, por lo tanto, la rentabilidad de la pieza final.
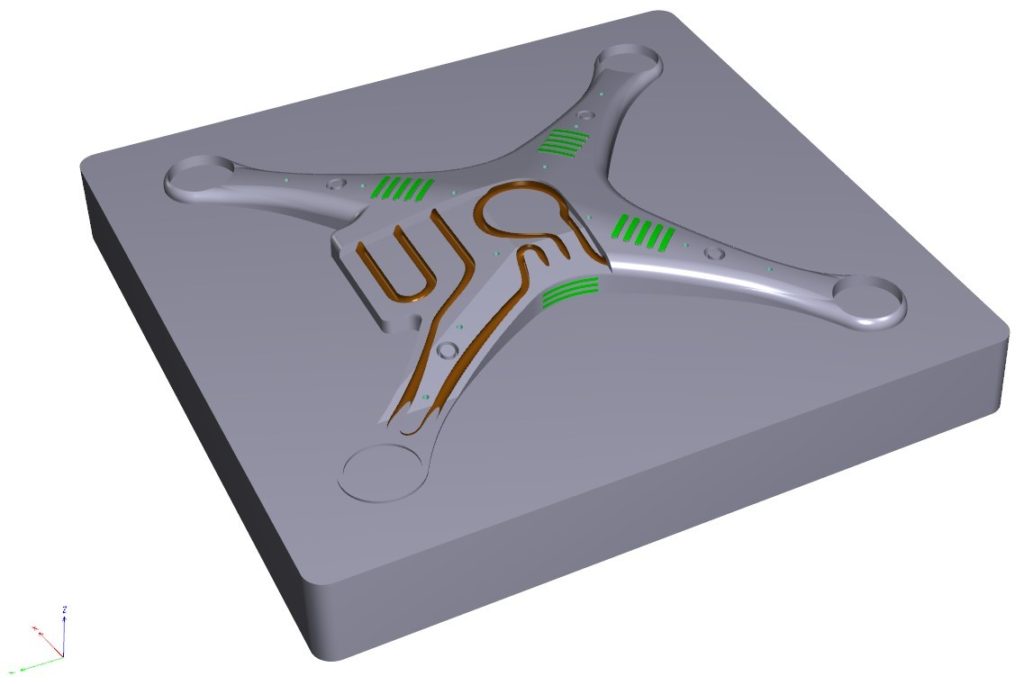
El enfriamiento del molde con técnicas tradicionales implica la perforación de canales de refrigeración en los insertos del molde. La limitación de los canales perforados es que deben seguir líneas rectas. Un mejor enfoque es el uso de canales de enfriamiento conformes, llamados así porque los canales siguen de cerca, o se ajustan, a la forma de la pieza que se está moldeando. Debido a que los canales están ubicados a distancias constantes de la superficie de moldeo, hay más uniformidad de temperatura (mejorando la calidad) así como también mejor enfriamiento general (para tiempos de ciclo más cortos).
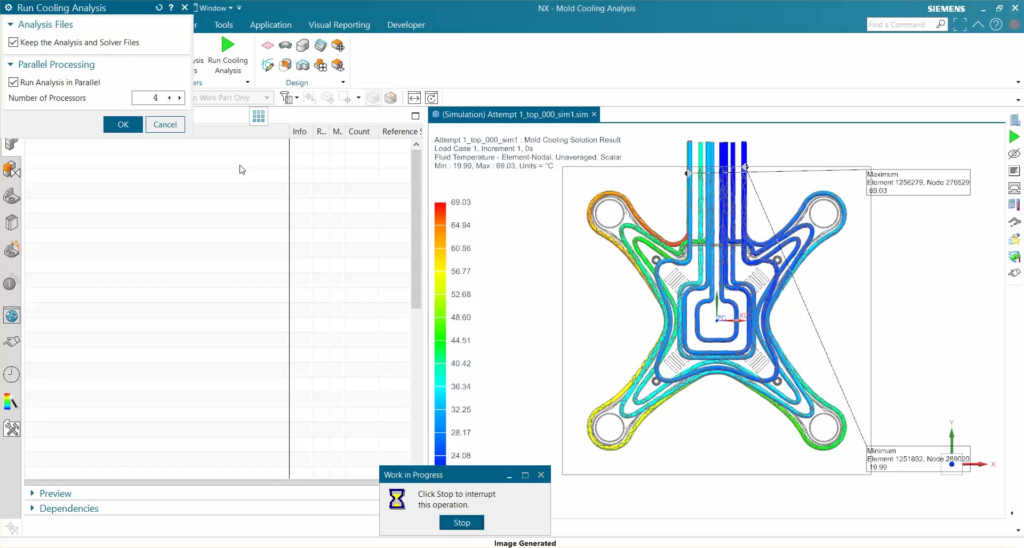
La fabricación aditiva es la tecnología que hace posible el enfriamiento conforme, y Siemens proporciona toda la funcionalidad necesaria para la fabricación aditiva de moldes, desde el diseño hasta la impresión y la validación posterior a la impresión. Al diseñar los canales de conformación para el molde del cuadricóptero, tuvimos acceso a una funcionalidad especial dentro de NX que permite características avanzadas como estructuras de celosía, que aumentan la vorticidad del fluido para una mejor transferencia de calor por convección.
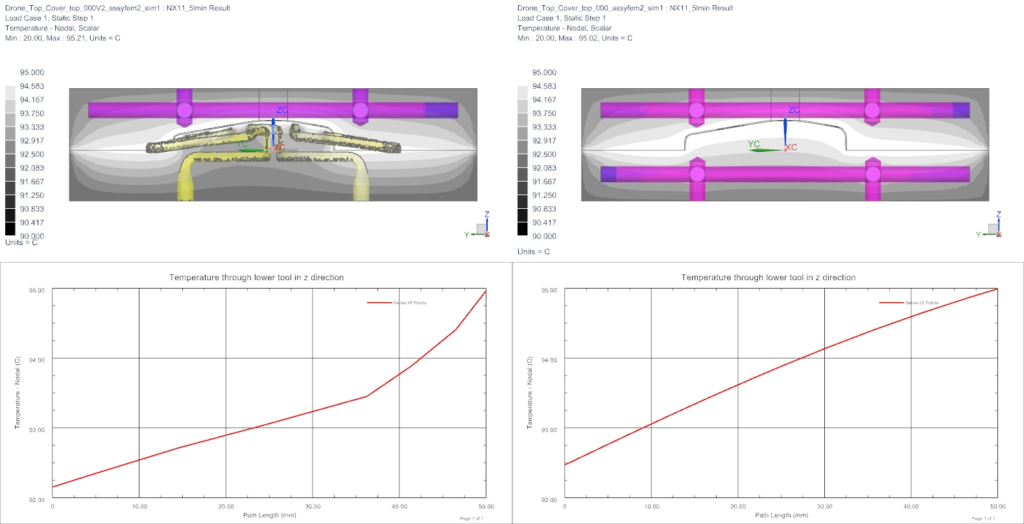
Para imprimir el molde final, usamos el modelo NX, junto con dos soluciones de Siemens, NX Additive Manufacturing y Simcenter 3D for AM, para configurar la operación de fabricación aditiva, simularla y optimizarla en software, y luego programar el proceso (metal fusión de lecho de polvo en una máquina Stratasys) que creó el molde con los canales de enfriamiento conformes.
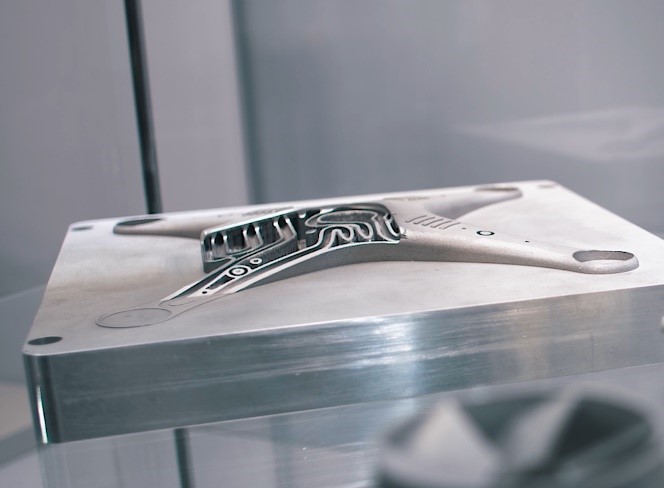
La primera tarea fue la preparación de la construcción, un paso fundamental para obtener resultados de fabricación aditiva de calidad. Aquí, aprovechamos las herramientas de preparación de compilación integradas dentro de NX Additive Manufacturing para agilizar este paso.
Luego, transferimos el modelo a Simcenter 3D para AM, lo que nos permitió simular y optimizar el proceso de construcción para que obtuviéramos la impresión correcta la primera vez. Después de definir los parámetros del proceso (material, número de piezas, corte de capas, parámetros del láser, etc.), ejecutamos la simulación, que mostró la distribución de temperatura y la distorsión en un gemelo digital de la pieza impresa. Luego, transferimos las distorsiones de la pieza a la geometría inicial para predeformarla mediante potentes técnicas de modificación de geometría basadas en el modelo de representación de límites (BREP). El nuevo archivo de pieza compensado se utilizó en la bandeja de construcción en lugar del original, lo que garantiza una construcción precisa del molde y sus canales de enfriamiento. El paso final involucró operaciones de fresado de alta precisión utilizando el software NX CAM para terminar la pieza.
Fabricación aditiva para la reparación de moldes
Aunque esto no era parte del proyecto del cuadricóptero, quiero mencionar brevemente otro uso de la fabricación aditiva para moldes: para reparar daños, como puntos desgastados. En este caso de uso, se utilizan procesos de fabricación aditiva para acumular material en el punto desgastado, seguidos de operaciones CNC para fresar y pulir esa área después de la construcción.
Hoy en día, este proceso híbrido ahora es posible en una sola máquina, lo que simplifica enormemente la reparación de moldes. La DMG MORI Lasertec 65, por ejemplo, realiza soldadura por deposición láser 3D y fresado de 5 ejes. El software Siemens NX CAM es compatible con las máquinas Lasertec, proporcionando programación para las trayectorias láser (de fabricación aditiva) así como las trayectorias de corte (de mecanizado sustractivo). Las máquinas híbridas como esta permiten que las reparaciones de moldes se realicen con una sola configuración, lo que significa un ahorro significativo de tiempo y costos.