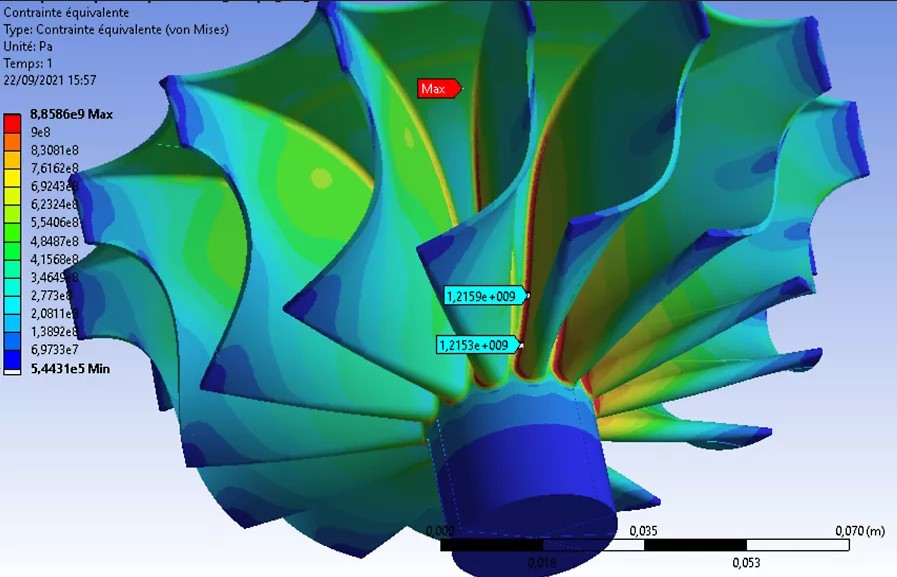
Turbotech impulsa la aviación sostenible con soluciones de propulsión eficientes y basadas en la simulación
Los principales retos a la hora de desarrollar sistemas de propulsión eficientes para aviones ultraligeros y ligeros -vehículos con un peso máximo de despegue de aproximadamente 1.250 libras- incluyen el equilibrio entre el tamaño, el peso y la potencia, al tiempo que se optimiza el consumo de energía para reducir el gasto de combustible.
Pero Turbotech, un fabricante aeronáutico con sede en Francia, está utilizando la simulación multifísica de Ansys a través del programa Ansys Startup para desarrollar sistemas de propulsión de alta potencia y bajo consumo para vehículos aéreos ultraligeros y ligeros.
Como primera empresa del mundo en introducir turbinas regenerativas para aplicaciones aeronáuticas, Turbotech ofrece soluciones de vuelo sostenibles con turbinas tan eficientes como los motores de pistón tradicionales. El ingrediente principal de este revolucionario motor es el característico intercambiador de calor de Turbotech.
Gracias a la innovadora tecnología del intercambiador de calor y a la continua integración de la simulación de Ansys, Turbotech está impulsando a las pequeñas aeronaves hacia un futuro más limpio con productos pioneros, como el primer turbopropulsor de bajo consumo de combustible, los primeros turbogeneradores para aeronaves híbridas-eléctricas y la próxima turbomáquina impulsada por hidrógeno.
Turbotech despega
Fundada en 2017, Turbotech carecía de recursos y necesitaba acceder a herramientas de simulación sofisticadas. Gracias a la colaboración con Ansys, la empresa pudo iniciar el desarrollo y hoy sigue beneficiándose del software de simulación de Ansys.
«Nuestra relación con Ansys ha sido vital para el éxito de Turbotech como empresa y también de nuestros productos», afirma Jean-Michel Guimbard, director de tecnología de Turbotech. «El programa Ansys Startup nos dotó de las herramientas y los recursos que necesitábamos para lanzar nuestro negocio, y hoy en día, como cliente, seguimos seleccionando las herramientas estándar de la industria de Ansys para acelerar el diseño de nuestros productos e informar mejor nuestras decisiones de ingeniería para proporcionar sistemas de propulsión de próxima generación para la industria de la aviación de aviones ultraligeros y de deportes ligeros.»
Tras conectar con Ansys, Turbotech integró rápidamente Ansys Mechanical, Ansys Fluent y Ansys CFX en su flujo de trabajo. Su primer desarrollo, y el más esencial para los productos posteriores, fue su característico intercambiador de calor de microtubos.
Utilizando Mechanical para los análisis estructurales y térmicos, los ingenieros observaron la temperatura y la presión. El equipo identificó los valores de la tensión y la deformación del intercambiador de calor para aproximarse al diseño y determinar el número de ciclos (es decir, cada parada y arranque del motor) que podría gestionar en su vida útil. La mayoría de las iteraciones se realizaron en Mechanical para evaluar el comportamiento en fuertes gradientes térmicos, mientras que CFX se utilizó para analizar el flujo de los tubos y las pérdidas de presión de los manómetros.
El intercambiador de calor de Turbotech es más ligero y compacto que los intercambiadores de calor tradicionales, pero puede recuperar el calor que normalmente se desperdicia en los gases de escape y reinyectarlo en la cámara de combustión, lo que supone una importante reducción de combustible.
Basándose en esta tecnología, Turbotech ha desarrollado el primer turbopropulsor regenerativo con el modelo TP-R90, capaz de desarrollar hasta 136 caballos de potencia, y los primeros turbogeneradores equipados para aviones híbridos-eléctricos con dos modelos, el TG-R55 y el TG-R90, para una potencia de funcionamiento continuo de 55 y 90 kilovatios, respectivamente. Los turbohélices son adecuados para aviones pequeños, helicópteros y vehículos aéreos no tripulados (UAV), también conocidos como drones, mientras que los turbogeneradores son aptos para aviones híbridos y aviones híbridos eléctricos de despegue y aterrizaje vertical (eVTOL).
Al construir primero el prototipo de turbopropulsor, los ingenieros utilizaron Mechanical para realizar análisis armónicos de las vibraciones que podrían afectar al motor de turbina o a sus componentes, incluidos los engranajes, el eje, el compresor y las ruedas de la turbina. Aplicando CFX y sus herramientas integradas para el diseño de álabes, la aeromecánica y el modelado de turbulencias, el equipo examinó los componentes aerodinámicos, desde las pérdidas de presión en la cámara de combustión hasta el giro de las ruedas. Para el turbogenerador, el grupo siguió el mismo diseño, añadiendo una máquina eléctrica de accionamiento directo en lugar de una caja de cambios para proporcionar una alta densidad de potencia.
Otras consideraciones en el diseño de la turbomaquinaria son la longevidad y el tiempo entre revisiones (TBO), que es el número de horas de funcionamiento sugerido por el fabricante antes de que un motor de avión u otro componente requiera una revisión. Tanto el turbopropulsor como el turbogenerador de Turbotech tienen un impresionante TBO de 3.000 horas.
La simulación permite a los ingenieros determinar estas medidas y combatir dos de las principales formas de deterioro de las turbinas: la oxidación y la fatiga. El control de la temperatura es clave para evitar la oxidación, mientras que el análisis térmico adicional ayuda a comprender la carga cíclica para evitar la fatiga y determinar el TBO y el número de ciclos que puede soportar.
«Con Ansys Mechanical, podemos llegar a esos valores con bastante precisión y saber que podemos confiar en ellos porque los modelos de Ansys son conocidos por su precisión», afirma Guillaume Malet, ingeniero de diseño de Turbotech. «Además, la realidad y la experiencia confirman los valores que extraemos del software, por lo que una vez que conocemos las características de fatiga y la tensión máxima alternativa de nuestros materiales, con los modelos de Ansys podemos diseñar las piezas adecuadamente para que se ajusten a eso y saber que tenemos un diseño que es robusto y puede aguantar ese número de horas o ciclos.»
Impulsar un futuro más eficiente
Al integrar la simulación de Ansys, Turbotech aceleró el desarrollo del producto cinco veces, completando el prototipo de cada producto en unos dos años. El considerable ahorro de tiempo, sumado al apoyo de Ansys, se tradujo en un ahorro de costes paralelo.
«La simulación de Ansys y el programa Ansys Startup nos ayudan a ahorrar tiempo y dinero, ya que hace algunos años se habrían necesitado docenas y docenas de prototipos, pero hemos podido tener nuestros productos funcionando de forma eficiente y sin problemas después de sólo unos pocos prototipos», dice Malet. «Sin las herramientas de simulación de Ansys, si tuviéramos que diseñar bancos de pruebas para cada componente, tardaríamos hasta 10 años en poder hacer funcionar este tipo de motores de forma eficiente y sin problemas».
Un prototipo anterior de turbopropulsor experimentó repetidos fallos de alto ciclo. Utilizando el análisis estático para observar la deformación, el equipo descubrió que la causa era la vibración y simuló cómo el recorte del álabe podía reducir o eliminar el problema. El diseño actualizado se montó, se probó y empezó a funcionar con éxito en un mes.
En la actualidad, Turbotech está optimizando aún más sus productos con hidrógeno para impulsar una nueva línea de productos, BeautHyFuel. El primer producto de la línea es un turbopropulsor diseñado para funcionar con hidrógeno y soportar el almacenamiento criogénico a bordo.
Para rediseñar el turbopropulsor para este uso, el equipo implementó Fluent y CFX para modelar el flujo de gotas de la combustión de queroseno y establecer una línea de base para el comportamiento y la temperatura. A continuación, modificaron el sistema de inyección y la cámara de combustión. También redujeron significativamente el tiempo de cálculo utilizando las capacidades de mallado de Fluent. El grupo utilizará los mismos métodos para modificar su turbogenerador. Turbotech seguirá ofreciendo sus líneas originales, que funcionan con queroseno o combustible de aviación sostenible, pero en los próximos años ofrecerá los nuevos productos alimentados con hidrógeno para los clientes que busquen una eficiencia aún mayor.
Sin embargo, según Malet, la eficiencia va más allá del combustible, y subraya que el diseño aerodinámico y la instalación precisa del motor son igualmente importantes para crear una relación potencia-peso favorable. Por ejemplo, un motor diésel podría funcionar de forma eficiente en términos de combustible, pero podría pesar 700 libras y requerir revisiones frecuentes, lo que reduciría su longevidad, además de necesitar un sistema de refrigeración pesado. Por ello, Malet sostiene que la eficiencia debe tener en cuenta la ligereza, la robustez y la fiabilidad, además del combustible.
Futuros vuelos
A medida que Turbotech se adentra en la tecnología aeronáutica de próxima generación, lleva consigo la simulación de Ansys. En otro proyecto próximo, Turbotech planea integrar las herramientas electromagnéticas de Ansys para diseñar una máquina eléctrica altamente optimizada para alimentar el turbogenerador.
«Necesitas las herramientas de simulación adecuadas para conseguir el diseño más optimizado, y sin Ansys, nunca habríamos podido diseñar una rueda de compresor con alta eficiencia aerodinámica y saber cómo podría comportarse en términos de vibración», dice Malet. «El mayor reto es conseguir una herramienta eficaz y fácil de usar que te ayude con el diseño. Una vez que dominas la teoría, pasas a la práctica y necesitas las herramientas adecuadas para ayudarte».
Para obtener más información, visite el sitio web de Turbotech. Para saber más sobre el programa Ansys Startup, haga clic aquí.