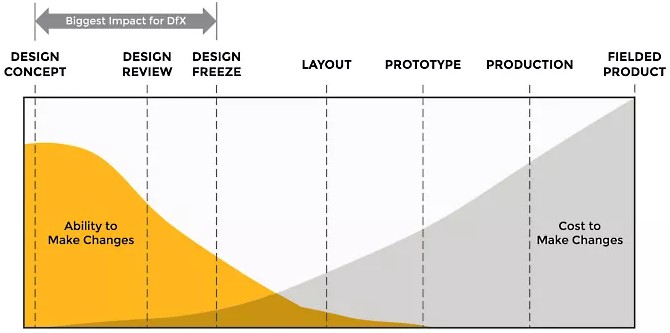
¿Qué es el Diseño para la Excelencia (DfX)?
Los ingenieros hablan a menudo de la importancia del diseño para la excelencia (DfX) y del impacto que tiene en el tiempo total de comercialización de un producto, la fiabilidad sobre el terreno y la satisfacción del cliente. El DfX puede tener un impacto significativo en el éxito de una empresa y de un diseño, y merece la pena conocer sus metodologías y cómo pueden aplicarse. Echemos un vistazo a los fundamentos del DfX y a cómo las empresas pueden emplearlo para su mayor beneficio.
El diseño para la excelencia es un enfoque sistemático y proactivo del diseño que utiliza los conocimientos y la experiencia de los expertos en otras partes del proceso de desarrollo del producto (por ejemplo, pruebas, fabricación, operaciones y asistencia) para garantizar que el producto final pueda realizarse con un coste del ciclo de vida razonablemente bajo sin dejar de cumplir los objetivos de fiabilidad, calidad, durabilidad y expectativas del cliente.
El diseño para la excelencia se basa en la premisa de que diseñar un producto correctamente desde el principio es mucho menos costoso que encontrar un fallo más adelante en el desarrollo del producto o a nivel del cliente. Al evaluar cuestiones que van más allá de la funcionalidad básica del producto en una fase temprana del diseño, los que aplican un enfoque sólido de DfX consiguen reducciones significativas de defectos, desechos, repeticiones de trabajo y pruebas, y aumentan el rendimiento del producto.
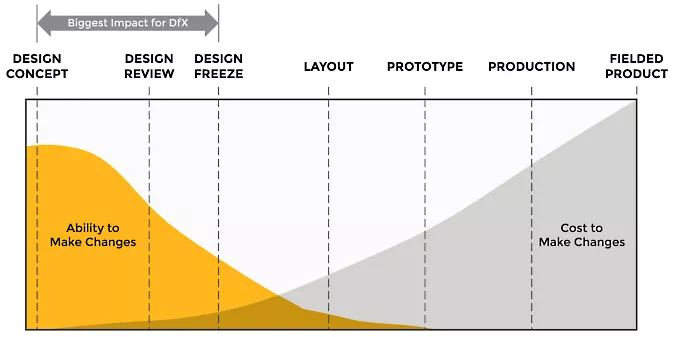
Beneficios de DfX
Diferenciación del producto: A medida que las tecnologías electrónicas alcanzan la madurez, hay menos oportunidades de diferenciar los productos de la competencia mediante métricas tradicionales como el precio y el rendimiento. Los enfoques DfX permiten a las empresas mantener bajos los costes de producción y asistencia al tiempo que consiguen una fiabilidad y durabilidad impresionantes que hacen las delicias de sus clientes.
Garantía de fiabilidad: Los circuitos avanzados, los sofisticados requisitos de potencia, los nuevos componentes, las nuevas tecnologías de materiales y las piezas menos robustas hacen que garantizar la fiabilidad sea cada vez más difícil. La aplicación de un enfoque DfX que incluya programas bien pensados de diseño para la fiabilidad (DfR), diseño para el entorno de uso (DfE) y diseño para pruebas (DfT) disminuye significativamente el coste de garantizar la fiabilidad y reduce el riesgo de fallos inesperados en las pruebas o sobre el terreno.
Control de Coses: Aunque varía en función del producto, normalmente alrededor del 70% del coste de un proyecto de introducción de un nuevo producto viene determinado por el concepto de diseño seleccionado. Cuando se completa el proceso de diseño, ya se ha fijado hasta el 95% del coste del ciclo de vida del producto. Los cambios de diseño a partir de ese momento son costosos y repercuten negativamente en el coste del programa de preproducción y en los plazos de lanzamiento del producto.
Con el enfoque DfX, las empresas pueden aplicar la experiencia y las lecciones aprendidas de la fabricación, el montaje, las pruebas, el embalaje, el mantenimiento y la reparación, los entornos de uso real y otras áreas no relacionadas con el diseño para minimizar los costes de diseño, fabricación y soporte.
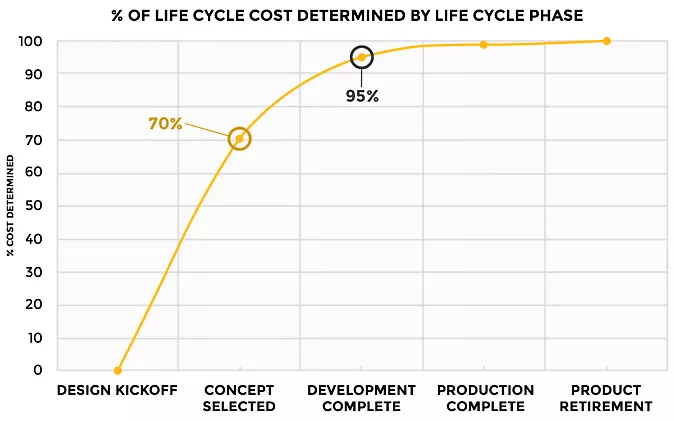
Acelerar el tiempo de comercialización: Especialmente en mercados altamente competitivos, llegar rápidamente al mercado con un producto que los clientes quieren y necesitan es fundamental para adelantarse a la competencia y captar cuota de mercado. Llegar rápido al mercado y ser reconocido por ofrecer uno de los mejores productos del mercado puede ser un difícil equilibrio que se facilita con una estrategia DfX eficaz.
El rediseño, los fallos en las pruebas y los problemas de montaje y fabricación roban un tiempo valioso al calendario de introducción del nuevo producto. Los enfoques DfX aportan al diseño una filosofía de ingeniería concurrente que tiene en cuenta las necesidades de cada fase de desarrollo del producto con el fin de crear un diseño que fluya a través de las fases previas al lanzamiento con un mínimo de obstáculos relacionados con el diseño.
¿Cuándo se usa el DfX?
Los principios DfX pueden aplicarse en cualquier momento del ciclo de vida del producto en el que tenga lugar el diseño, incluidos el diseño inicial y el rediseño. Por supuesto, para cualquier introducción de un nuevo producto (NPI), las prácticas DfX deben aplicarse lo antes posible en la fase de diseño. En el caso de un producto ya comercializado o de un producto que ya se encuentra en otras fases de su desarrollo, nunca es demasiado tarde para considerar los enfoques DfX cuando surge la necesidad de rediseñarlo.
Introducción de nuevos productos: Debido al coste percibido o al miedo a ahogar la creatividad y la innovación, puede haber cierta resistencia a aplicar DfX en la fase inicial de concepto de un diseño, pero es fundamental incorporar especialistas en DfX y las lecciones aprendidas lo antes posible para maximizar los beneficios. Incluso en la fase conceptual, es importante plantearse preguntas como:
-
- ¿Qué impacto tendrá el diseño en la fiabilidad?
-
- ¿Habrá que inventar una nueva tecnología para hacer realidad este diseño?
-
- ¿Qué retos de fabricación plantea este diseño?
-
- ¿Cómo se prestará asistencia al producto implantado?
Aunque estas consideraciones están muy lejos del diseño conceptual, pueden ser cruciales para las compensaciones del concepto de diseño y para que la fase de diseño se inicie en la dirección correcta. Como mínimo, el programa DfX debe estar en pleno funcionamiento antes de que se establezcan los requisitos detallados del diseño.
Producto a medio desarrollar: Si un producto ha superado ampliamente la fase de diseño pero experimenta problemas en la preproducción, las pruebas o la fabricación que requieren un rediseño, las prácticas DfX pueden ayudar a garantizar que el próximo rediseño sea el último. Aplicar los conocimientos de DfX en esta fase ayuda a identificar las verdaderas causas que impulsan el rediseño y da como resultado un diseño más adecuado para ser probado, fabricado, ensamblado, desplegado, reparado, etc.
Producto de campo: Los productos de campo que se rediseñan como parte de un programa proactivo de mejora del producto o para abordar problemas de fiabilidad, rendimiento, mantenimiento o seguridad sobre el terreno también pueden beneficiarse de las prácticas DfX. Identificar las causas de cualquier problema y desarrollar los requisitos para el rediseño son tareas clave en las que la metodología DfX puede tener el mayor impacto para minimizar el coste y el plazo del esfuerzo de rediseño.
¿Quién debe implicarse en DfX?
Aunque los enfoques DfX requieren el conocimiento de expertos, los equipos de diseño de éxito se aseguran de que todos los miembros del equipo comprenden, aplican y ven el valor de la metodología DfX. Los equipos DfX de éxito captan y utilizan los conocimientos de los expertos en forma de requisitos de diseño, reglas de diseño y formación de los miembros del equipo para garantizar que todos los miembros del equipo utilizan las mejores prácticas DfX. Para que los expertos ayuden a abordar problemas novedosos, deben ser incluidos en los hitos críticos del diseño para ayudar a identificar riesgos y desarrollar estrategias de mitigación.
Dependiendo del tamaño y la estructura de la organización, los puestos de trabajo pueden variar, pero los participantes clave en el programa DfX deben tener experiencia en la selección y abastecimiento de componentes, física de la fiabilidad, montaje y fabricación, pruebas, prácticas y logística de apoyo sobre el terreno, y entornos de uso y factores de estrés. Dependiendo del producto y de su uso previsto, también pueden ser útiles los conocimientos en áreas como la gestión térmica, la normativa medioambiental aplicable, la seguridad, la reutilización y el reciclaje, y la gestión de costes.
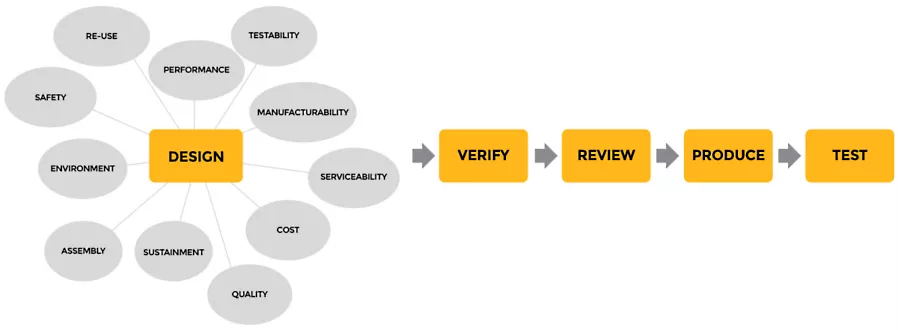
Buenas Prácticas en DfX
Empezar pronto. La aplicación de prácticas DfX en una fase temprana del proceso de diseño genera productos de mayor calidad con un menor coste del ciclo de vida y plazos de comercialización más cortos. Cuanto más espere, menor será el impacto de DfX en el producto final.
Personas, procesos y herramientas. Empezar de cero no es fácil. Un programa sólido de DfX requiere:
- Personas con los conocimientos adecuados, formación y una mentalidad de mejora continua.
- Procesos bien documentados, de fácil acceso y estandarizados que incorporen las mejores prácticas y las lecciones aprendidas.
- Herramientas estándar que facilitan la aplicación de conocimientos expertos a todos los miembros del equipo de diseño. De hecho, un programa DfX bien diseñado debería suponer menos herramientas en su proceso de diseño en lugar de más.
Utiliza sólo lo que necesites. Dependiendo de a quién pregunte, existen casi 50 prácticas de DfX diferentes. La buena noticia es que sólo se necesitan unas pocas para influir positivamente en el proceso de desarrollo del producto. El diseño para la fiabilidad (DfR), el diseño para la fabricabilidad (DfM), el diseño para la comprobabilidad (DfT) y el diseño para la sostenibilidad (DfS) son las prácticas DfX más comunes en la industria electrónica. Si no utiliza una metodología DfX en la actualidad, considere la posibilidad de implantar una sola de estas técnicas de eficacia probada.
You May Also Like
Ansys Discovery | Usando Block Recording para parametrizar un modelo 3D en Discovery Modelling
La parametrización de un modelo 3D puede resultar muy útil para estudiar distintas configuraciones
Reduce costes en pruebas físicas garantizando la eficiencia de la válvula de control mediante la simulación
La simulación desempeña un papel clave en el diseño de una válvula de control con una capacidad
NX CAD | Creación y gestión de unidades
Muchas veces necesitamos que nuestras medidas se tomen en una determinada unidad, así nos ahorramos