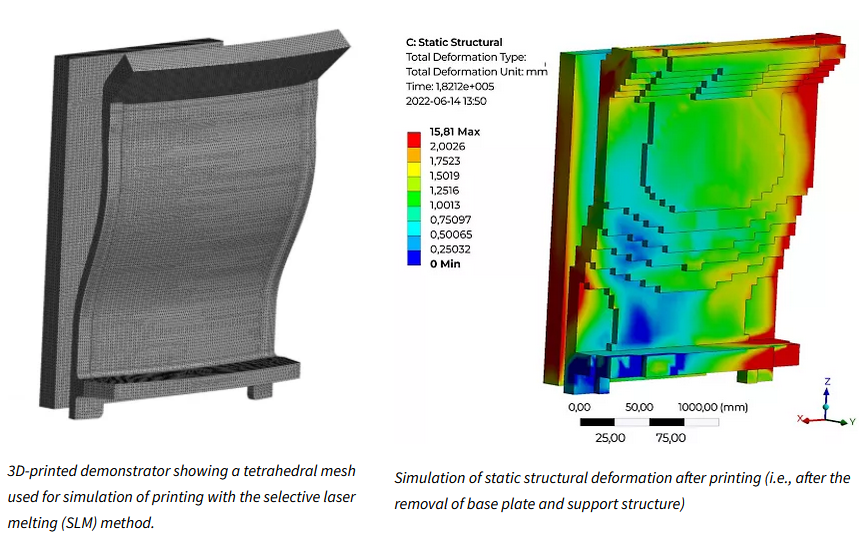
Deshazte de los errores, no de los materiales, con la simulación
La fabricación aditiva (FA) promete ser una de las mayores tendencias en la fabricación sostenible. Las nuevas prácticas de diseño, como la optimización de la topología, dan como resultado piezas optimizadas mucho más ligeras, lo que se traduce, por ejemplo, en vehículos más ligeros y mayor eficiencia de combustible. Durante el proceso de impresión 3D, se crea una pieza mediante la fusión, unión o fusión de una cantidad prescrita de material para respaldar los esfuerzos hacia un entorno sin desperdicios. Eso no quiere decir que la impresión 3D no sea un desperdicio: la impresión de formas requiere soportes o estructuras que eviten la deformación de una pieza durante el proceso de impresión, lo que resulta en una cantidad nominal de material desechado. Pero, ¿qué sucede en el caso de impresiones fallidas?
Los ingenieros pueden desechar potencialmente una cantidad significativa de piezas y materiales para lograr el éxito durante la fase de diseño. A menudo, los errores se solucionan solo después de que se identifica una pieza defectuosa al final del proceso de fabricación, junto con darse cuenta de que continuar imprimiéndola no es una opción. Es posible que la mayoría de los fabricantes aún no conozcan las metodologías de diseño de fabricación aditiva, y confiar en un enfoque de prueba y error para la impresión no es práctico. El uso del software Ansys permite a Combitech, una empresa de consultoría independiente que opera principalmente en la región nórdica, ayudar a sus clientes a identificar los problemas del proceso de impresión que conducen a impresiones fallidas de piezas a través de la simulación.
Demostrador impreso en 3D que muestra una malla tetraédrica utilizada para la simulación de impresión con el método de fusión selectiva por láser (SLM).
“Nosotros hacemos el trabajo de diseño y simulamos el proceso de producción a nivel de pieza”, dice Tomas Sjödin, Jefe de Ingeniería Asistida por Computadora (CAE) y Análisis en Combitech. “Para algunos clientes, solo hacemos el trabajo de diseño, y para otros clientes, solo hacemos el trabajo de simulación del proceso de producción. En otros productos, simulamos el rendimiento de la pieza real en sí, considerando variables como la rigidez, la fatiga o la resistencia”.
La línea entre el éxito y el fracaso
La idea de simular la producción surgió de los métodos de trabajo bien establecidos de Combitech para la verificación del diseño de chapa, que implica simulaciones de conformado de chapa. Además de lograr un diseño de producto final, la metodología garantiza que un producto cumpla (y pueda fabricarse con éxito teniendo en cuenta) los requisitos del cliente. De manera similar, Combitech aumentó su actividad dentro de AM para optimizar la producción para sus clientes. Inicialmente querían poder simular un ciclo de producción real en la impresora 3D para identificar cualquier problema durante el proceso de impresión que condujera a la falla. Junto con Ansys, Combitech ha llevado a cabo una serie de proyectos para fortalecer su competencia en esta área.
“Entre nuestros clientes vemos un mayor uso de la impresión 3D, tanto para ahorrar tiempo como para aumentar el rendimiento”, dice Sjödin. “Vengo de la industria automotriz y he estado trabajando mucho con piezas de carrocería y chapa. Por cada pieza de automóvil estampada que se fabrica, hay una simulación de estampado de chapa metálica antes de que se produzca, sin excepciones. Esto es para encontrar y resolver cada problema antes de ordenar las herramientas. Estamos utilizando la misma estrategia para la impresión 3D: antes de enviar cada pieza a la impresora, se debe simular el proceso para evitar fallas en la impresión antes de que comience la producción”.
Distribución térmica transitoria de la pieza de construcción con la estructura de soporte y la placa base para la impresión con el método de fusión selectiva por láser (SLM)
Cuando la precisión se reduce a una fracción de milímetro
Utilizando las soluciones de simulación de Ansys, Combitech ha llevado a cabo un proyecto de investigación y dos proyectos industriales en la industria de la defensa. Uno de estos proyectos requería el uso de fusión selectiva por láser (SLM), una forma de AM que requiere un láser de densidad de alta potencia para fundir y mezclar polvos metálicos. Este método se usó en una pieza que incluía canales de enfriamiento para mantener propiedades mecánicas específicas y enfriar la electrónica. Cada canal de enfriamiento se midió hasta 1 milímetro de diámetro. Otro requisito era que la superficie debería ser plana hasta 0,1 milímetros, descartando el fresado como opción después de la impresión.
El gran desafío fue lograr una geometría detallada que requería una malla muy fina con largos tiempos de simulación. En este escenario, el equipo de Sjödin quería ver si Ansys Additive Suite podía manejar estas altas demandas de precisión. El objetivo general era implementar cambios en la geometría para lograr una menor distorsión y satisfacer la demanda de la geometría final en una pieza con una superficie muy plana. Inicialmente, esto fue un desafío para el cliente: la primera parte que imprimieron tenía una desviación de superficie de 1 milímetro.
Usando varias herramientas en Additive Suite, la geometría se importó como archivos STEP y los datos de la máquina se recopilaron del operador de la impresora. Posteriormente, el equipo comparó los resultados de la simulación con los datos escaneados. Las capacidades de integración de Additive Suite fueron críticas para el éxito general de Combitech, permitiéndoles importar sin problemas la geometría de la pieza desde los archivos STEP para su análisis. También usaron sus propios scripts para comparar los datos escaneados de piezas reales con los resultados de las simulaciones, lo que les ayudó a identificar las causas de las fallas de impresión y llegar a una solución diferente para sus clientes.
El procesamiento previo y posterior se realizó en computadoras portátiles de ingeniería en Windows; sin embargo, todos los análisis de diseño se realizaron en el clúster de Linux con la cantidad adecuada de CPU. Debido a la geometría detallada, los ingenieros tuvieron que usar una malla muy fina que requería largos tiempos de simulación para lograr menos distorsión y cumplir con los requisitos del cliente para la geometría final.
Demostración impresa en 3D utilizando el método de deposición de metal por láser basado en polvo (LMD-P), que muestra la distribución térmica transitoria después de la impresión.
Additive Suite reduce los costos del cliente
El equipo de Sjödin también logró el éxito utilizando Additive Suite para un proyecto de fabricación aditiva de arco de alambre (WAAM) más pequeño que involucró la deposición de metal por láser (LMD), una técnica de deposición de energía directa que a menudo se usa para imprimir piezas metálicas en 3D o agregar características a una estructura metálica existente. . Durante este proceso, se usa un láser de alta potencia para derretir una superficie metálica mientras se deposita simultáneamente un polvo metálico o alambre. Junto con el cliente, el equipo quería investigar la posibilidad de simular el proceso WAAM con un producto más pequeño y un método de impresión diferente al que se usaba anteriormente. Con la ayuda de Additive Suite, el equipo logró capturar el fenómeno general y ganar confianza en el método, los resultados, las herramientas y el tiempo necesarios para la fabricación de una aplicación ligeramente diferente.
“Los resultados son muy prometedores para Ansys Additive Suite en la captura de fenómenos físicos que ocurren en la realidad”, dice Sjödin. “Estoy convencido de que las simulaciones del proceso de fabricación para AM se convertirán en un trabajo estándar en el futuro, de la misma manera que lo es hoy en día la simulación del conformado de chapa. Mediante el uso de simulaciones de Ansys, podemos reducir la cantidad de piezas fallidas y podemos corregir un diseño antes de que cueste a nuestros clientes más tiempo y dinero en la impresión 3D”.
Las herramientas de Ansys, incluido Additive Suite, han mejorado drásticamente la calidad general de las piezas y han acelerado el proceso de desarrollo para los clientes de Combitech. Con estas herramientas, Combitech continuará estableciendo nuevos estándares de calidad para la producción con simulación que genera soluciones más livianas y de bajo desperdicio para productos aeroespaciales, médicos, de transporte, energéticos, de consumo y más.