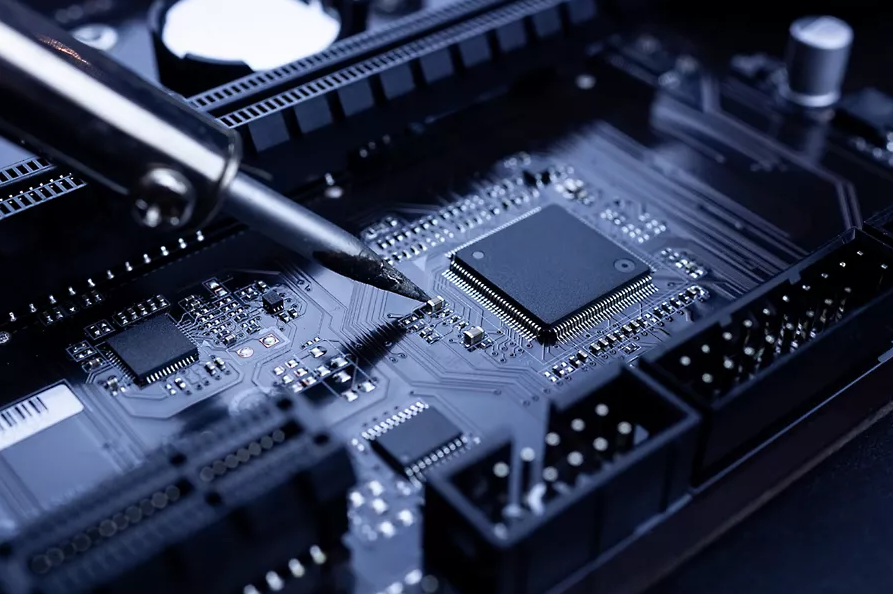
Como planear y ejecutar tests HALT (Highly Accelerated Life Testing)
Evaluar la robustez de un producto electrónico es esencial para el éxito de su diseño y rendimiento. Los ensayos de vida útil altamente acelerados (HALT) son una importante herramienta de ensayo para este fin, y su eficacia puede maximizarse mediante una cuidadosa planificación previa a la configuración y una ejecución detallada.
¿Qué es HALT?
HALT es el proceso de aplicar mayores cargas a un dispositivo electrónico para forzar fallos y descubrir puntos débiles de diseño y construcción. Los factores de estrés aplicados suelen ser muy superiores a los entornos de campo previstos para descubrir rápidamente los fallos. Esto permite a los ingenieros optimizar los diseños, reparar o sustituir los componentes defectuosos y reducir los costes de desarrollo del producto.
Desarrollo de un plan HALT
Establecer expectativas y directrices claras para llevar a cabo la HALT es un proceso de varios pasos que comienza con la reunión de los ingenieros de diseño para:
- Desarrollar un plan de pruebas basado en la física de la fiabilidad, que incluya la comprensión de los posibles modos y mecanismos de fallo y la definición clara de los objetivos.
- Determinar los entornos previstos, incluidas las tensiones aplicables, como la temperatura, las vibraciones y los choques.
- Decidir cuántos dispositivos bajo prueba (DUT) están disponibles para las pruebas. Por lo general, se utilizan de una a cinco muestras.
- Seleccione las pruebas funcionales que se realizarán durante las pruebas, como qué debe hacer el dispositivo, qué circuitos deben estar activos y qué códigos y sensores deben recopilar datos.
- Determinar qué parámetros deben controlarse en función de las pruebas funcionales deseadas y de la aplicación.
- Definir qué constituye un fallo. Por ejemplo, no superar una prueba funcional (controlada de forma continua o periódica durante la prueba), observar daños físicos, no permanecer operativo, etc.
- Considere la posibilidad de utilizar software de simulación de fiabilidad para simular las cargas térmicas y de vibración, de modo que pueda crearse un modelo que pueda alcanzar los límites HALT.
Junto con el desarrollo del esquema básico, deben abordarse dos áreas clave.
1. Tensiones aplicables
Seleccione las tensiones y los niveles de tensión adecuados para las pruebas:
- Vibración
- Alta temperatura
- Baja temperatura
- Margen de tensión/frecuencia
- Ciclos de potencia
- Tensiones combinadas (es decir, temperatura y vibración)
La elección de las tensiones adecuadas depende de la aplicación y del entorno en el que funcione el dispositivo. Las partes sospechosas o las áreas de preocupación dentro del dispositivo también pueden ayudar a determinar qué niveles de estrés aplicar en la prueba.
2. Enfoque de tensión por pasos
Para cada esfuerzo previsto, delimite claramente:
- El punto de tensión inicial.
- La cantidad en que se incrementará la tensión prevista en cada paso.
- La duración de cada paso.
- El límite del dispositivo o equipo para ese esfuerzo.
Tensiones escalonadas aplicadas en HALT.
Normalmente, los límites operativos y destructivos del dispositivo no se conocen antes de la prueba. Las pruebas HALT pueden utilizarse para determinarlo mediante el enfoque de tensión escalonada. Si se produce un fallo durante las pruebas de control o funcionales, la tensión se reduce posteriormente hasta que el DUT se recupera del fallo. Este fallo se conoce como límite operativo. Cuando la tensión se incrementa por encima del límite operativo y el DUT ya no puede recuperarse sin una reparación, se ha alcanzado el límite de destrucción.
Configuración de una prueba HALT
Para obtener resultados precisos, debe prestarse especial atención a la configuración de la HALT:
- Diseñe un dispositivo de vibración para garantizar que la energía vibratoria se transmite al producto.
- Diseñar conductos de aire para garantizar que la energía térmica se transmite al producto. Esto puede incluir la modificación del DUT para permitir un flujo de aire sin obstáculos en el interior del dispositivo.
- Ajuste la cámara a la muestra que se va a probar.
- Determine la ubicación de los termopares y los acelerómetros para controlar la temperatura y la aceleración, respectivamente.
- Instale todo el equipo de ensayo funcional y el cableado.
Realización de una prueba HALT
La prueba HALT es exhaustiva y abarca varias fases de ensayo, cada una de ellas con parámetros específicos a seguir.
Estrés térmico escalonado
Las pruebas de estrés térmico escalonado aplican niveles de estrés de temperatura incrementales a lo largo del ciclo de vida del producto con el fin de identificar los modos de fallo del producto.
- Conecte el equipo de prueba funcional y de alimentación a los DUT. Dependiendo de la aplicación, pueden aplicarse o no tensiones adicionales específicas del producto.
- Comience con la tensión escalonada en frío, seguida de la tensión escalonada en caliente.
- Utilice inicialmente incrementos de 10 °C, disminuyendo a incrementos de 5 °C a medida que se aproxima a los límites.
- Fijar el tiempo mínimo de permanencia en 10 minutos más el tiempo necesario para realizar una prueba funcional. La temporización debe comenzar una vez que la temperatura que se controla en el DUT haya alcanzado su punto de ajuste.
- Continúe la prueba hasta que se determinen los límites de funcionamiento y destrucción, o la tensión máxima según lo dictado por el plan de prueba.
Ciclos de choque térmico
Los ciclos de choque térmico se realizan entre los límites de funcionamiento del DUT determinados anteriormente. Esto expone al DUT a transiciones térmicas rápidas, a veces de 60 ˚C por minuto o tan rápido como lo permita el equipo/cámara de pruebas.
- Conecte el equipo de ensayo funcional y de alimentación a los DUT. Dependiendo de la aplicación, pueden aplicarse o no tensiones adicionales específicas del producto.
- Mantenga el intervalo de temperatura entre 10 °C por debajo del límite superior de funcionamiento y 10 ˚C por encima del límite inferior de funcionamiento determinado durante la prueba de esfuerzo escalonado.
- Si la muestra no puede soportar las transiciones térmicas máximas, disminuya la velocidad de transición en 10 °C por minuto hasta encontrar la velocidad admisible.
- Continúe las transiciones térmicas en caliente y en frío con intervalos de 10 minutos en cada extremo durante un total de cinco ciclos.
Esfuerzo por pasos de vibración
Las pruebas de estrés por vibración escalonada aplican niveles de estrés por vibración incrementales con el fin de identificar los modos de fallo del producto.
- Conecte la alimentación y el equipo de pruebas funcionales a los DUT. Dependiendo de la aplicación, pueden aplicarse o no tensiones adicionales específicas del producto (ciclos de potencia, márgenes de tensión/frecuencia de línea, etc.).
- Determine los incrementos del valor cuadrático medio (Grms) del nivel G, que suelen oscilar entre 3 y 5 Grms en el producto.
- Establezca el tiempo de permanencia mínimo en 10 minutos más el tiempo necesario para realizar una prueba funcional.
- A partir de 30 Grms, realice una vibración de «cosquilleo» entre las vibraciones de consigna. La vibración de cosquilleo se realiza a 5 Grms mientras se realiza la comprobación funcional.
- Continúe la prueba hasta que se determinen los límites de funcionamiento y destrucción, o el esfuerzo máximo según dicte el plan de pruebas.
Combine los ensayos de vibración y choque térmico
Combine los resultados de las pruebas y las metodologías para seguir probando los productos.
- Conecte los equipos de pruebas funcionales y de alimentación a los DUT. Dependiendo de la aplicación, pueden aplicarse o no otras tensiones específicas del producto (ciclos de potencia, márgenes de tensión/frecuencia de línea, etc.).
- Utilice el límite de destrucción por vibración y divídalo por 5 para determinar el incremento de paso en cada uno de los cinco ciclos térmicos para esta prueba.
- Utilice los límites de los ciclos de choque térmico y la velocidad de rampa para los cinco ciclos térmicos.
- A partir de 30 Grms, realice una vibración de «cosquilleo» entre las vibraciones de consigna (para manifestar modos de fallo no evidentes bajo amplitudes de vibración elevadas o condiciones estáticas). La vibración de cosquilleo se realiza a 5 Grms mientras se realiza la comprobación funcional.
Proceso posterior a HALT
Una vez finalizado el proceso HALT, los ingenieros de diseño se centran en determinar las causas de todos los fallos y las medidas correctivas. Esto puede incluir la identificación del lugar del fallo y el mecanismo de fallo para cada modo de fallo. Después, hay que realizar una HALT de verificación para evaluar si los ajustes de las pruebas han solucionado los problemas.