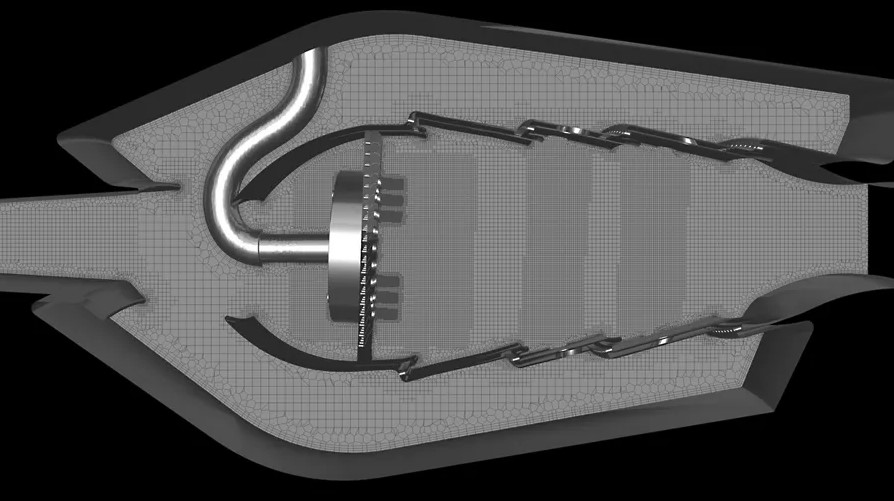
5 de las Mejores Prácticas para el mallado de la turbina de gas de hidrógeno
La Asociación Internacional de Transporte Aéreo (IATA) estableció el objetivo de reducir las emisiones de CO2 en un 50% en 2050 (en comparación con los niveles de emisión de 2005), sin que aumenten las emisiones netas después de 2020. También esperan que la demanda mundial de aviación se duplique hasta alcanzar los 8.200 millones de pasajeros al año en 2037. Estas cuestiones han llevado al sector de la aviación a centrarse en la transición del gas natural a los combustibles de aviación sostenibles (SAF), el hidrógeno y las mezclas de hidrógeno.
El hidrógeno, como alternativa a los combustibles fósiles, ofrece una densidad energética por unidad de masa notablemente alta, características de ignición superiores y un amplio límite de inflamabilidad. Sin embargo, presenta muchos retos, entre ellos:
- + Producción y almacenamiento
- + Estabilidad de la llama
- + Retroceso de llama
Las cámaras de combustión son geometrías complejas con características detalladas que pueden dar lugar a largos plazos de entrega para el proceso de mallado. Ansys Fluent acelera el mallado de geometrías grandes y complejas como las de las cámaras de combustión. Siguiendo nuestras cinco mejores prácticas, los usuarios podrán generar una malla de alta calidad que producirá resultados robustos y precisos.
Las cinco mejores prácticas para el mallado de turbinas de gas de hidrógeno utilizando Fluent son:
- Flujo de trabajo de geometría impermeable
- Mallado poli-hexcore mosaico con escalabilidad paralela
- Capas de inflación
- Resolución de malla por pieza
- Métricas de calidad objetivo
1. Flujo de trabajo de geometría impermeable
El flujo de trabajo de geometría estanca en Fluent acelera el mallado organizando el proceso en un flujo de trabajo basado en tareas fácil de usar. Este flujo de trabajo ofrece opciones relevantes, pero también tiene la flexibilidad de ser personalizado.
Las mejores prácticas están integradas en cada tarea para la calidad en forma de valores por defecto. Sin embargo, los usuarios avanzados pueden marcar fácilmente una casilla para revelar más opciones. También puede automatizar el proceso de mallado del flujo de trabajo de la geometría estanca utilizando un archivo de diario basado en Python para el mallado por lotes.
El uso de este flujo de trabajo garantizará una malla de alta calidad que genere resultados robustos para la mayoría de los casos de combustión de turbinas de gas de hidrógeno.
2. Mallado poli-hexcore mosaico con escalabilidad paralela
La tecnología de mallado Mosaic de Fluent acelera el tiempo de mallado y produce una solución más rápida y precisa. Esta tecnología permite realizar conexiones poliédricas entre tipos de malla dispares. Mosaic poly-hexcore es el primero en emplear esta tecnología y es una combinación de elementos poliédricos hexaédricos, isotrópicos y Mosaic.
Los elementos hexaédricos son deseados por su precisión y eficiencia. Dado que la malla del volumen del núcleo se genera utilizando elementos hexaédricos, el mallado para la misma resolución de malla da como resultado una reducción total del número de caras. Esto proporciona tiempos de cálculo más rápidos con menores requisitos de memoria y espacio en disco.
El mallado paralelo puede acelerar aún más el proceso de mallado de volúmenes. Tiene la capacidad de generar más de 10 millones de celdas por minuto cuando se ejecuta en 256 núcleos.
3. Capas de inflación
Para las simulaciones de combustión de turbinas de gas de hidrógeno, se utiliza el modelo de simulación de grandes remolinos (LES) en el dominio central. Dado que el LES no puede resolver con precisión las características del flujo cerca de las paredes, Fluent utiliza una simulación de resolución de escala híbrida, como la simulación de remolinos mezclados con tensión (SBES), con Reynolds-Averaged Navier-Stokes (RANS) cerca de las paredes.
Con RANS aplicado cerca de las paredes, nuestra tercera mejor práctica sugiere utilizar de tres a cuatro capas de inflación.
Este número ha demostrado dar resultados precisos a la vez que evita que las células se colapsen entre sí al pasar por pasos estrechos y pequeños orificios.
4. Resolución de malla por pieza
A continuación se puede ver un modelo genérico de la cámara de combustión de una turbina de gas de hidrógeno.
Debido a las complejas características de la cámara de combustión, se recomienda utilizar las mejores prácticas de resolución de malla para las siguientes partes:
- + Micromezclador o agitador
- Utilice un cuerpo de influencia (BOI) dentro del tubo del micromezclador con un mínimo de 20-25 celdas en todo el diámetro. También recomendamos extender el BOI en la sección caliente con una longitud equivalente a 3-4 veces el diámetro del tubo.
- + Núcleo del combustor
- Utilice BOI para generar una malla uniforme de alta calidad. Esto garantizará una transición suave de la malla desde el domo al núcleo y predecirá con precisión la mezcla, la forma de la llama y las emisiones.
- + Agujeros de dilución
- Tenga de 8 a 10 celdas a lo largo del diámetro del orificio de dilución para predecir con precisión los efectos de extinción
- + Zona de dilución
- La resolución en la zona de dilución puede ser más gruesa que en la zona primaria. Sin embargo, se recomienda utilizar un valor que sea el doble del tamaño de malla utilizado en el BOI del núcleo.
- + Componentes sólidos
- Si está modelando los componentes sólidos, le recomendamos que tenga 3 o 4 celdas en una sección transversal.
5. Calidad de la malla objetivo
La calidad de una malla desempeña un papel importante en la precisión y la estabilidad del cálculo numérico. El uso de las mejores prácticas enumeradas anteriormente debería dar como resultado una malla de alta calidad y lista para la simulación.
La calidad ortogonal de la celda se calcula utilizando la asimetría de la celda, el vector desde el centroide de la celda a cada una de sus caras, el vector de área de la cara correspondiente y el vector desde el centroide de la celda a los centroides de cada una de las celdas adyacentes. El valor oscila entre 0 y 1, donde 1 representa una calidad perfecta. El objetivo es una calidad ortogonal superior a 0,1.
La relación de aspecto equivale a una medida del estiramiento de una celda. Lo mejor es evitar cambios bruscos y grandes en la relación de aspecto de la celda en zonas donde el campo de flujo presenta grandes cambios o fuertes gradientes. Apunte a una relación de aspecto máxima baja al mallar su cámara de combustión.